The IntelliFlux APRICOT™ OPERATE software was installed at an MBR plant in Ningbo, China for a performance demonstration.
The objective was to optimize the performance of the membrane filtration system in the plant in response to influent water quality fluctuations and operating condition changes.
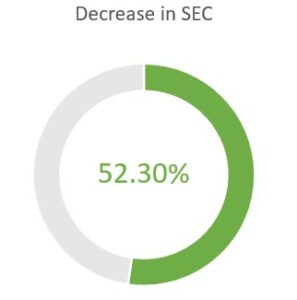
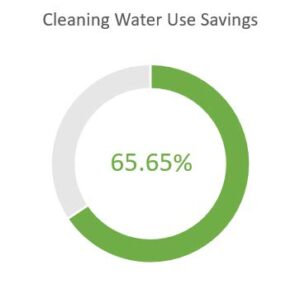
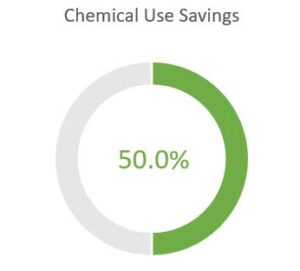
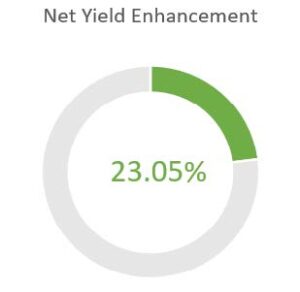
Percent changes of key performance indicators (KPI).
This optimization would help the plant find a balance between lower operation expenses (OpEx) and optimal membrane performance. This report summarizes the findings of the demonstration.
Application Area:
Wastewater Treatment
Customer:
Textile Processing Plant
Location:
China
System:
Membrane Bioreactor
Capacity:
2200 cubic meters/day
Operated:
2020-2021
Benefits:
Operating Energy Savings, Water Savings, Increase in Net Yield, Chemical Savings
IntelliFlux Controls, Inc. conducted a three-month demonstration of APRICOT™ OPERATE on a Membrane Bioreactor (MBR) system located at a textile facility in China. The plant was designed to have throughput of 2,230 m3/day, and was operated at an actual throughput of 800-1,200 m3/day.
IntelliFlux monitored the baseline performance of two MBR trains to evaluate system performance and the potential for APRICOT™ OPERATE to optimize the system. Next, one MBR train (“Train 2”) was retrofitted using IntelliFlux, while the other train (“Train 1”) was operated conventionally.
The study demonstrated the benefits of APRICOT™ OPERATE, which included energy savings, water savings, and chemical savings. Improvements were achieved in both production and reliability of the membrane system.
The benefits realized were:
- 52.3% savings in energy
- 65.7% savings in cleaning water
- 50% savings in chemical use
- 23.1% increase in net filtrate yield
Using real-time operational data, IntelliFlux predicted the best timing for triggering a backwash/Maintenance Clean (MC) and the optimal setpoints including flow rate and duration. Within setpoint ranges approved by the customer, IntelliFlux optimized the operation to trigger backwashes and MCs as needed.
For optimization, APRICOT™ OPERATE set up different intensities with differ-ent setpoints of backwash flow rate and durations. The software then dynamically selected different settings based on real-time evaluation of system performance and effectiveness of previous backwashes/cleans. The trigger was Permeability decay, which meant APRICOT™ OPERATE decided to run a back-wash when Permeability decreased by a certain percentage. By evaluating permeability decay, IntelliFlux was able.
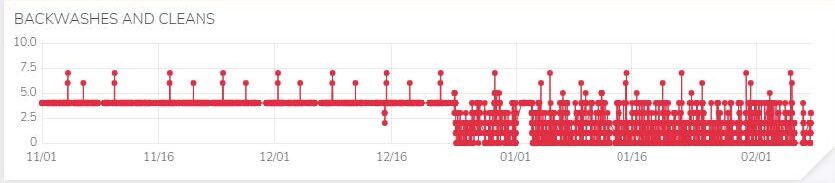
Cleaning intensity triggered before and after deploying APRICOT™
0-5 indicates backwashes (4 indicates the conventional settings), 6-7 indicates MCs
Although IntelliFlux was not able to adjust the detailed settings of MC with NaClO (sodium hypochlorite) or MC with citric acid, the frequency of conducting MC with NaClO was adjusted by APRICOT™ OPERATE within the given range. The frequency of MC with NaClO was twice a week under conventional mode, but it was reduced to 4 times per month under IntelliFlux control module.
During IntelliFlux control mode, no long-term decay was observed in Train 2’s permeability, and most filtration cycles were not showing typical decay cycles. This indicated that the membrane was still maintained very cleanly and similar to baseline observations, suggesting that we may have had more room to further decrease the cleans’ intensity and frequency.
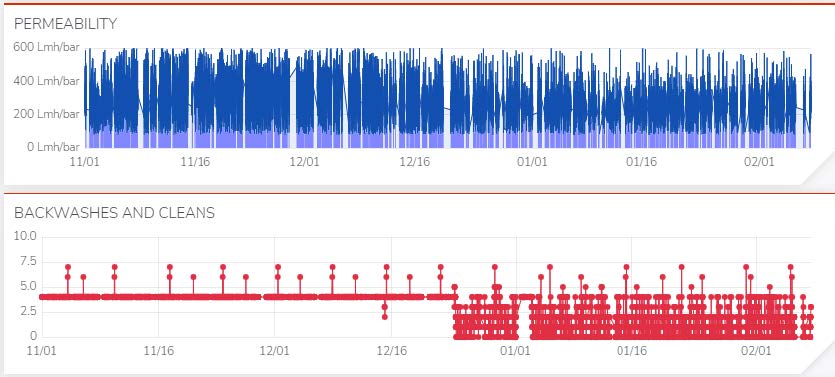
Is a very clean membrane good?
During baseline observations, the IntelliFlux team found that the permeability of both MBR trains were not showing typical decay during filtration. This suggested that the membranes were kept at a high level of cleanliness.
Keeping the membranes super clean would bring some issues. Maintaining high cleanliness (“overcleaning”) requires higher frequency of backwashes and cleans, which will consume more energy, cleaning water, and chemicals. In addition, the surface was directly exposed to chemicals during a Mainte-nance Clean (MC) or Recovery Clean, (RC) which could have decreased the membrane’s integrity.
Alternatively, too much fouling in the membrane will decrease membrane performance.
APRICOT™ by IntelliFlux will find an optimal middle ground between the two extremes to maintain and enhance the membrane’s lifetime, as well as de-crease water, energy and chemical use.
IntelliFlux improved the plant’s digitalization profile by implementing a digital twin, AI based Decision Support, and Automation layer with APRICOT™ OPERATE, improving the PLC/SCADA/IoT level system integration and performance. It was the lowest cost and quickest retrofit digitalization for the plant.
The KPI benefits were the results of lower intensity backwashes and lower frequency of both backwashes and MCs with NaClO, which would enhance the system capacity. Each benefit is shown in more detail, below with before-and-after comparisons of IF control mode initiation (Dec 23rd, 2020).
Train 2’s (IntelliFlux control mode) Specific Energy Consumption (SEC) was 0.015 kWh/m3, which was 52.30% lower than the baseline. The saving in cleaning energy consumption contributed the most to the total energy savings.
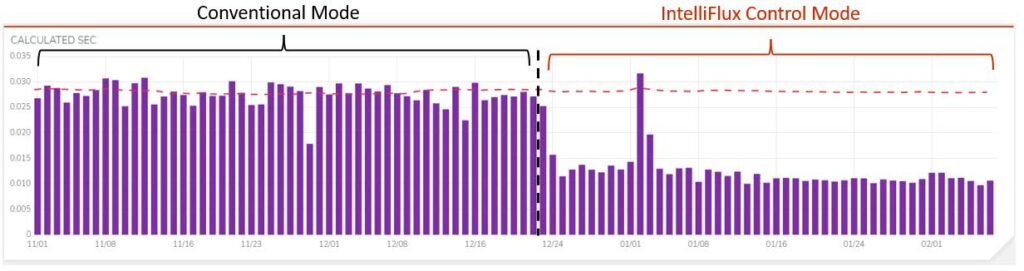
Cleaning water used was decreased by 65.65% during IntelliFlux control mode compared to the conventional mode.
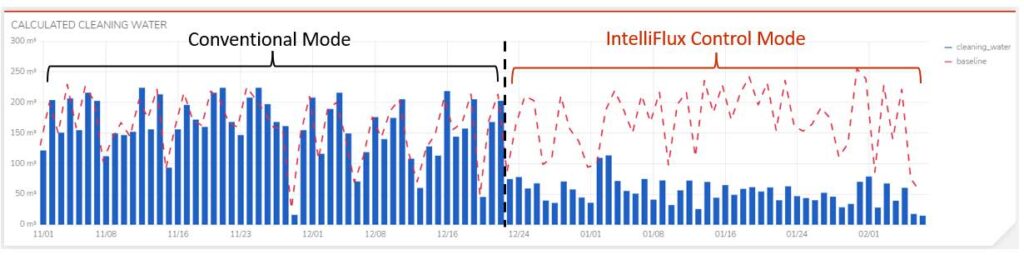
Due to cleaning water use savings, the net yield of Train 2 increased to 88.1%, which was 23.05% higher than the baseline.
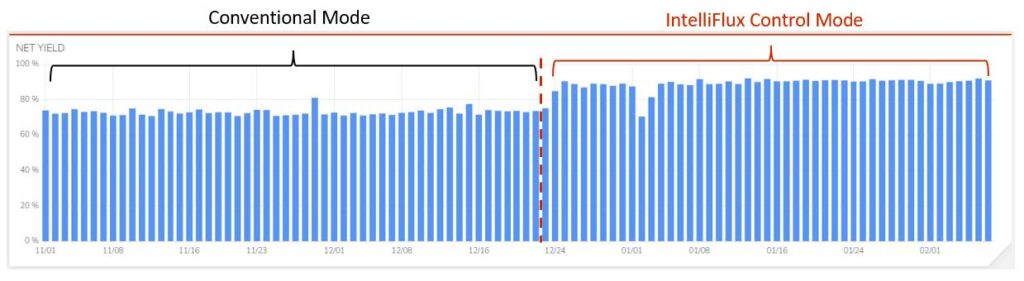
Since the frequency of MCs with NaClO decreased, the NaClO consumption of Train 2 was 50% lower that that in the baseline.
Extending the interval between MCs would further enhance the membrane lifetime. By allowing a proper fouling in the membrane system, the foulants accu-mulated on the surface, would protect the membrane from direct contact with chemicals such as NaClO, that might hurt the integrity of the membrane during MCs. Also, by minimizing contact of the membrane with NaClO, the membrane system’s reliability and sustainability will be enhanced while savings in chemical use will provide additional economic value.
Based on the analysis of the baseline operation data, IntelliFlux mode operation data, and the plant’s actual capacity, APRICOT™ OPERATE would bring even more benefits if some setpoint ranges could be further explored. For instance, if the range of the backwash frequency and MC frequency were extended, we could expect 60–85% greater savings in energy use, a 75—90% higher saving in cleaning water use, and p to 75% higher savings in chemical use while maintaining the system performance. Also, if the dosage of NaClO could be further adjusted within a given range and if the range of frequencies of both MCs could be extended to around twice per month, we would expect a 60—80% higher savings in NaClO use and an approximately 50% saving in Citric Acid Use.