Fast Track Digitalization
4 parts series to achieving a smart process plant
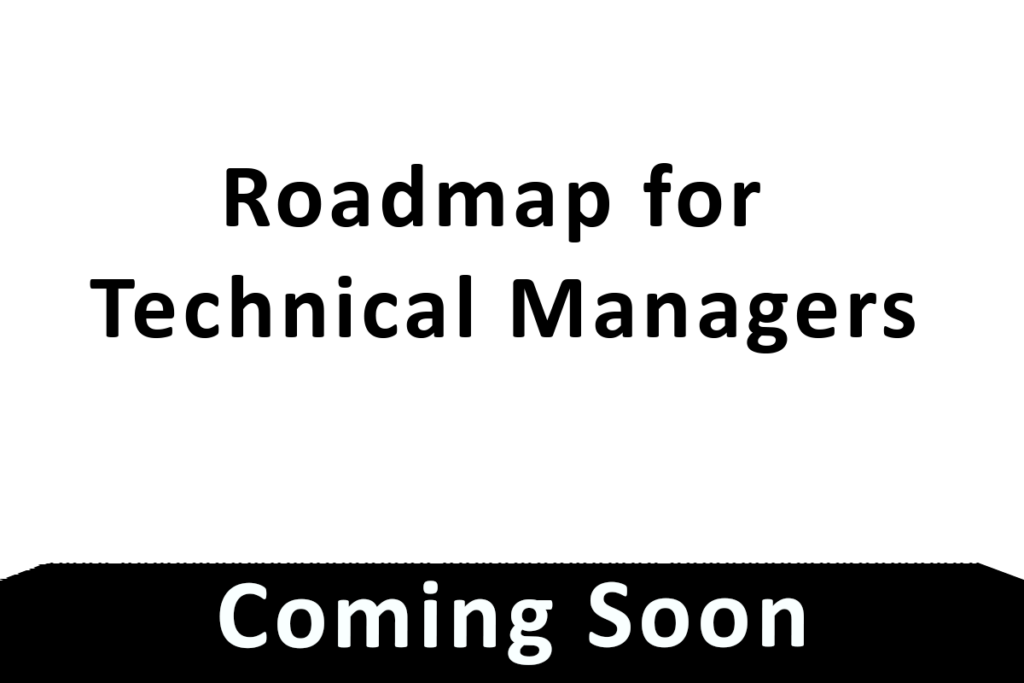
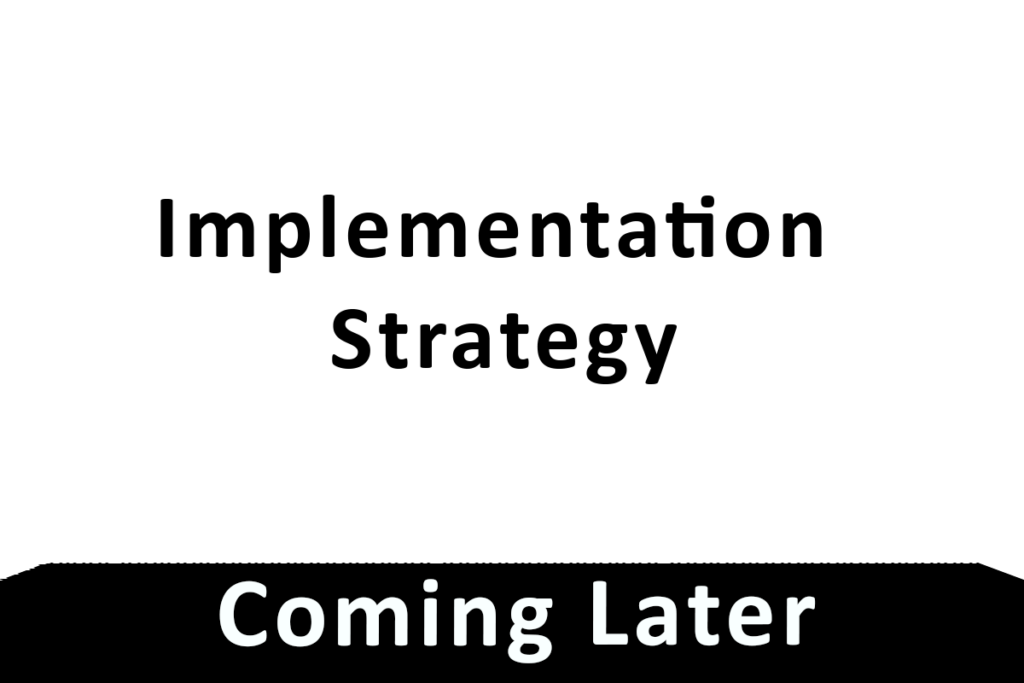
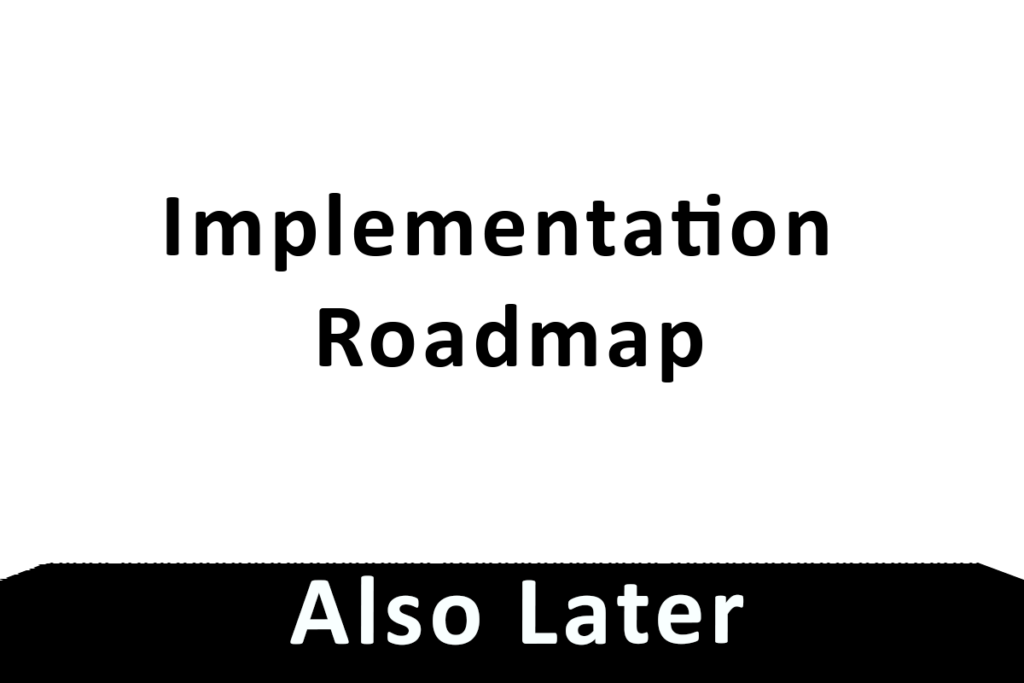
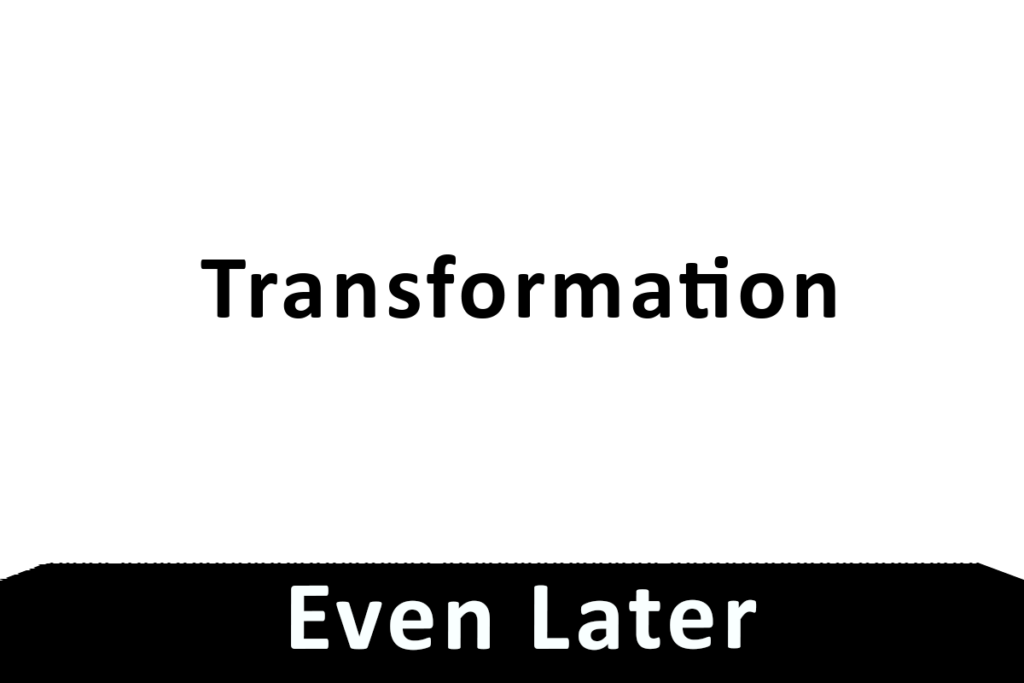
Fast Track Digitalization
4 parts series to achieving a smart process plant
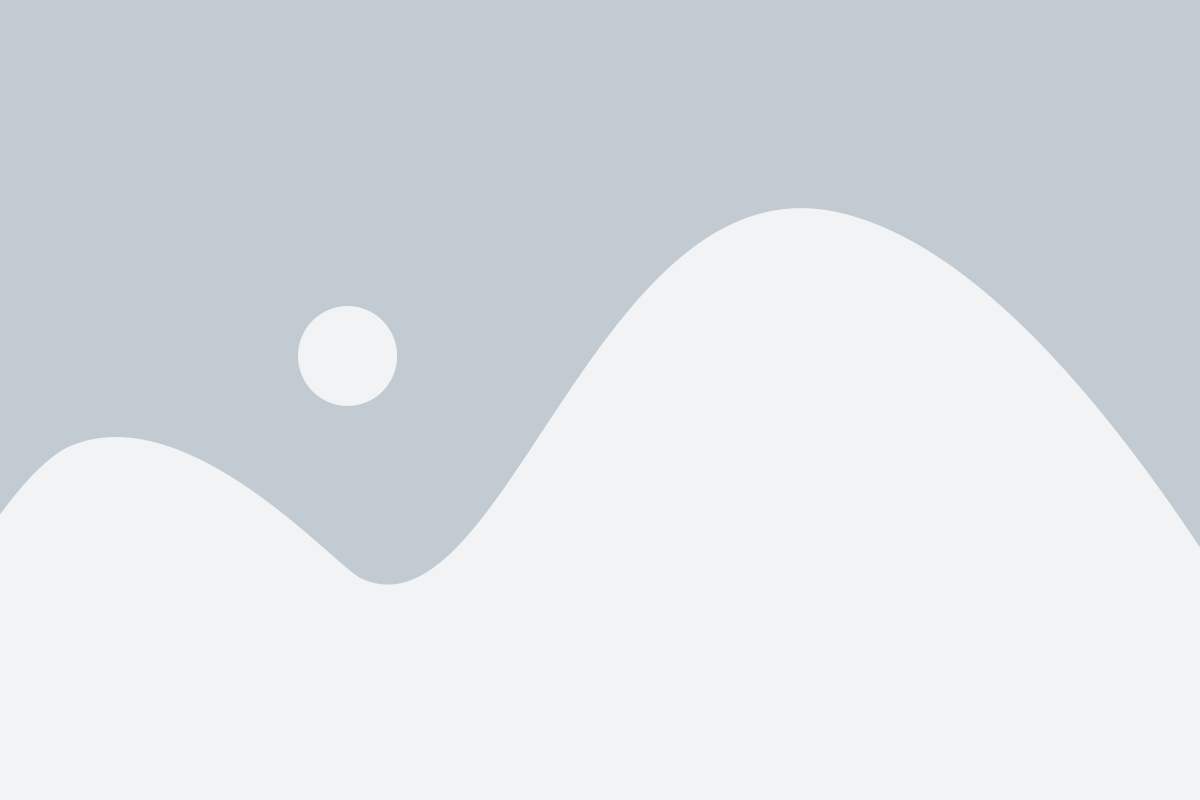
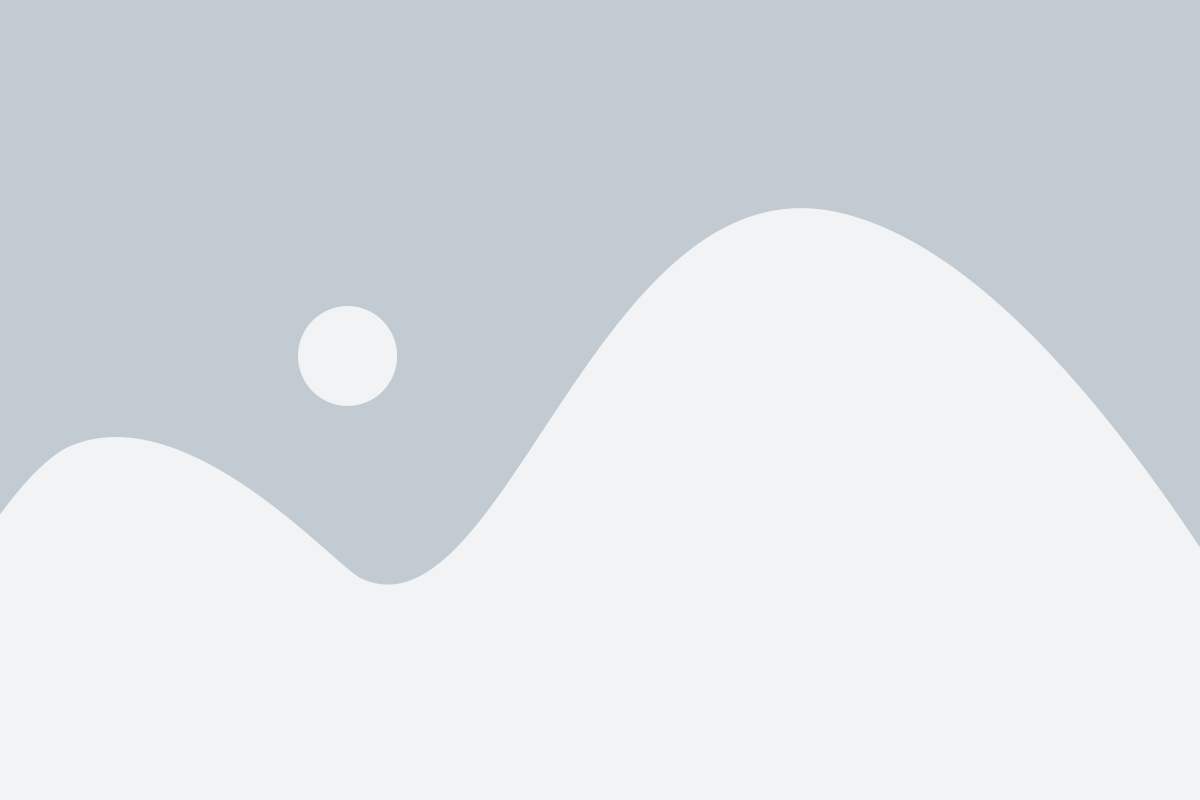
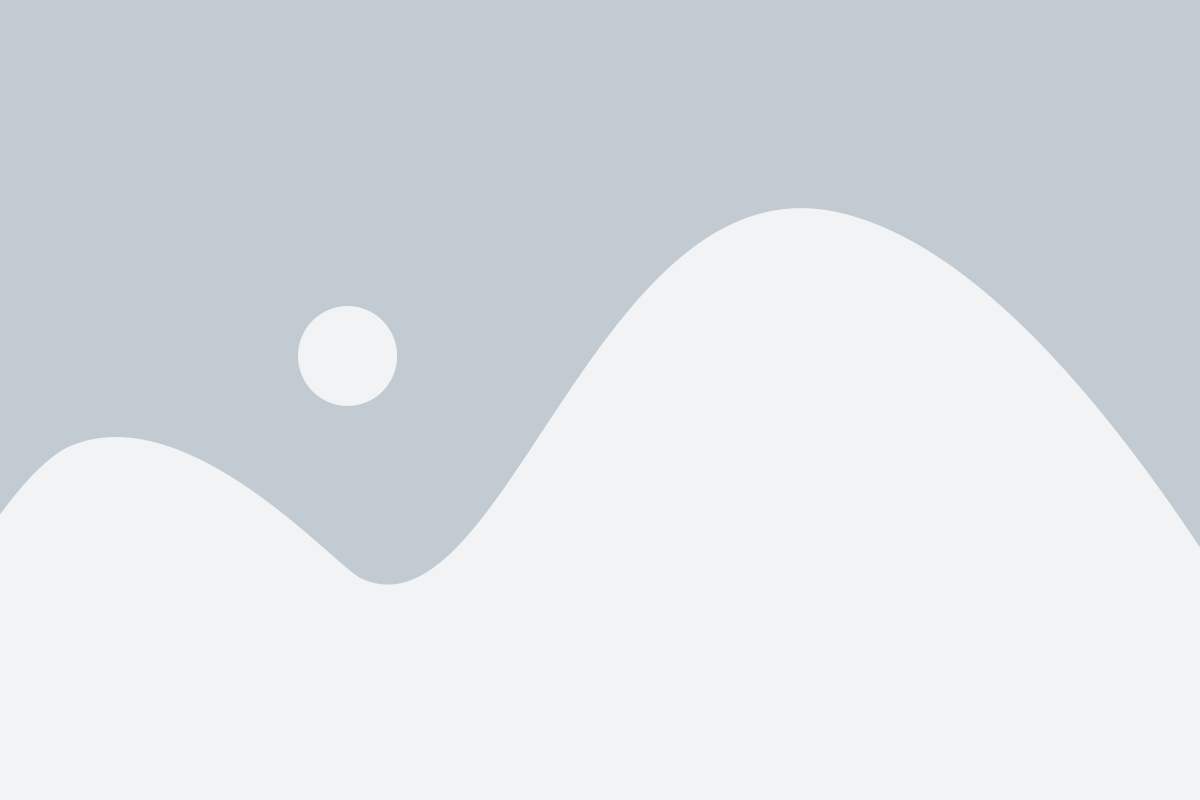
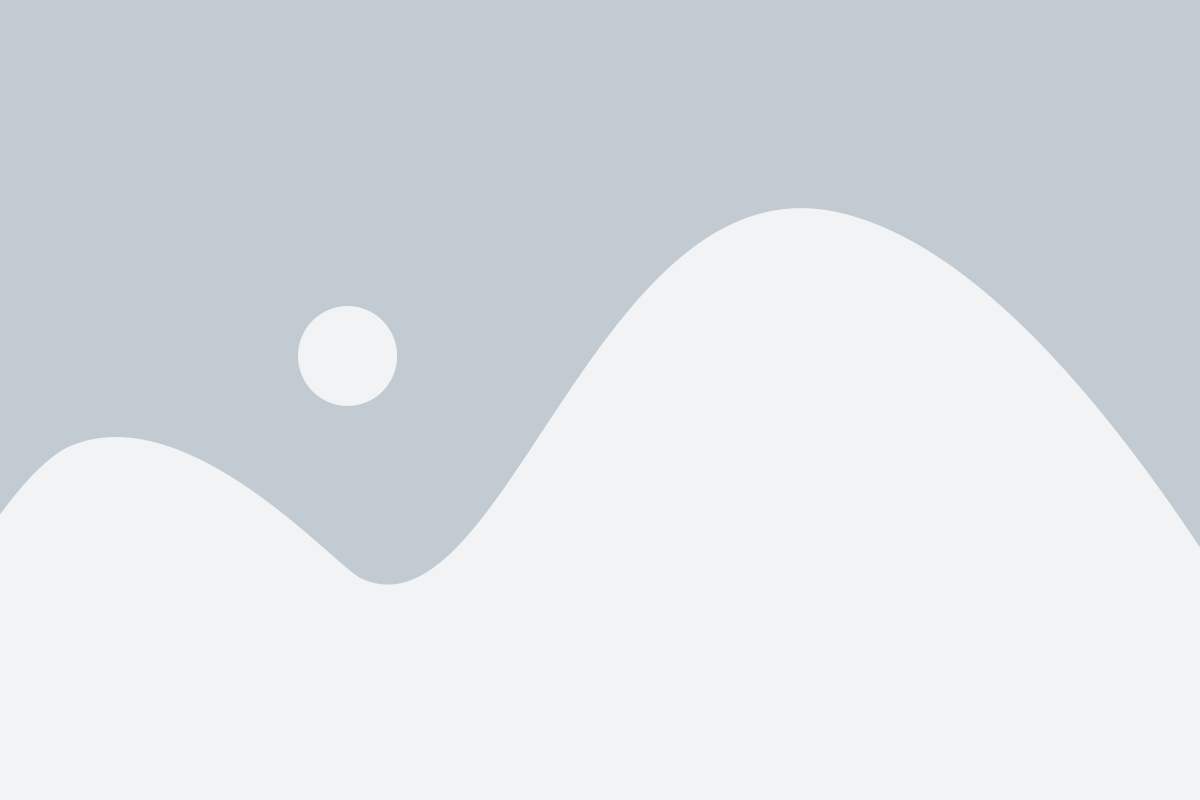
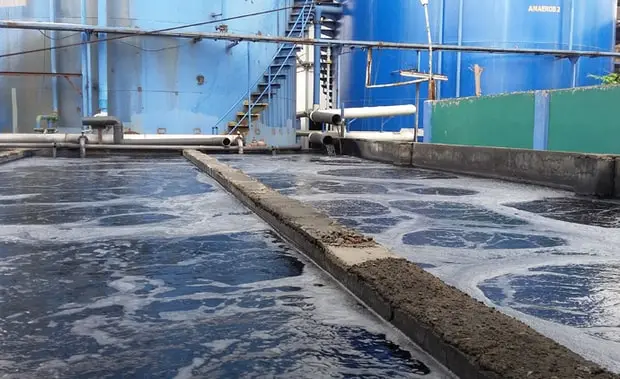
TEXTILE PROCESSING FACILITY OPTIMIZATION
Optimizing Facility Processes and Membrane Filtration
The IntelliFlux APRICOT™ OPERATE software was installed at an MBR plant in Ningbo, China for a performance demonstration.
The objective was to optimize the performance of the membrane filtration system in the plant in response to influent water quality fluctuations and operating condition changes.
The first step toward digital transformation of your process plant should be the asset that already exists at your plants – the automation programs and codes that currently run them. This article provides an overview of where these programs reside, what these programs are, and how to capitalize on them when you are planning on your plant’s digital transformation.
The desalination plant was retrofitted with APRICOTTM by IntelliFlux to optimize the performance of the coagulant dosing and multimedia filtration (MMF) operations in response to fluctuations in influent seawater quality. Resulting in 35% Chemical savings, 44% lower Specific Energy Consumption (SEC).
APRICOTTM by IntelliFlux was installed to optimize a treatment train including desilication chemical dosing, Inclined Plate Clarifier, UF and RO units through an integrated SCADA level automation platform with an objective of synergistically managing he precipitant dosage for the chemical desilication, monitoring the recycle rate of the UF to optimize the flosc for solid removal and managing the recovery of the RO process by maintaining a consistent RO feed quality. Click to see results.
Samples of biomass are collected from the biological reactors at the wastewater treatment plant. APRICOTTM by IntelliFlux embeds learning algorithms to recognize feartures in the microscopy images, links therese to the microbial population health and a relate these to the reactor operating conditions. The software immediately provides an assessment of the image, indicating the condition of the microcosm in the reactor, and recommendations for process management.
Process industry benefits to be gained from a digitalization initiative. What is digitalization? What are smart plants? Use of Internet of Things (IoT) and cyber-physical systems such as sensors, actuators, vision systems, and robotics to collect and use plant information in a real-time manner to increase production efficiency.
6000 bbl/day capacity walnut shell filtration system was retrofitted with APRICOTTM by IntelliFlux to optimize the filter performance and media cleaning process in response to fluctuations in influent produced water quality. Resulting in 47% energy reduction and 40% waste reduction in cleaning and ultimately a 5% increase in Uptime.
Replaces many sensors with a single one that can travel and take measurements at multiple locations on its own. The drone takes a pre-programmed flight path, stopping at locations where measurements need to be made. At each measurement site, the sonde is dipped into the desired depth of the tank or basin, the data reading is recorded and sent to a database with pro spatio-temporal signatures. Resulting in lower sensor cost and maintenance, less risk and more reliable results.
APRICOTTM by IntelliFlux was installed on a customer’s 15,000 m3/day capacity SBR as an automation retrofit to optimize the treatment performance and increase the throughput of the system. IntelliFlux utilized the system’s inline COD, TSS, Turbidity, NO3-N2, and Dissolved Oxygen (DO) sensors. Resulting in 28% increaase in Throughput and 45% savings in Energy per cycle
Retrofit Digitalization—Code of Process Plant
The first step toward digital transformation of your process plant could be to direct attention to an invaluable asset already exist at your plants. the automation programs and codes that currently run them. This article provides an overview of where these programs reside, what these programs are, and how to capitalize on them when you are planning on your plant’s digital transformation.
Retrofit Digitalization—Code of Process Plant
Outlines the benefits to be gained by the process industry from a planned digitalization initiative. What is digitalization? We are smart plants?
Industry 4.0 envisions the use of Internet of Things (IoT) and cyber physical systems such as sensors, actuators, vision system and robotics to collect and use plant information in a realtime manner by manufactureres to increase production efficiency.
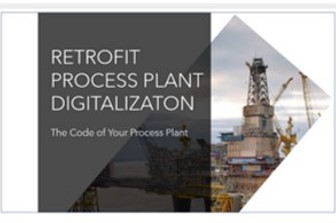
Retrofit Digitalization—Code of Process Plant
The first step toward digital transformation of your process plant could be to direct attention to an invaluable asset already exist at your plants. the automation programs and codes that currently run them. This article provides an overview of where these programs reside, what these programs are, and how to capitalize on them when you are planning on your plant's digital transformation. Learn More
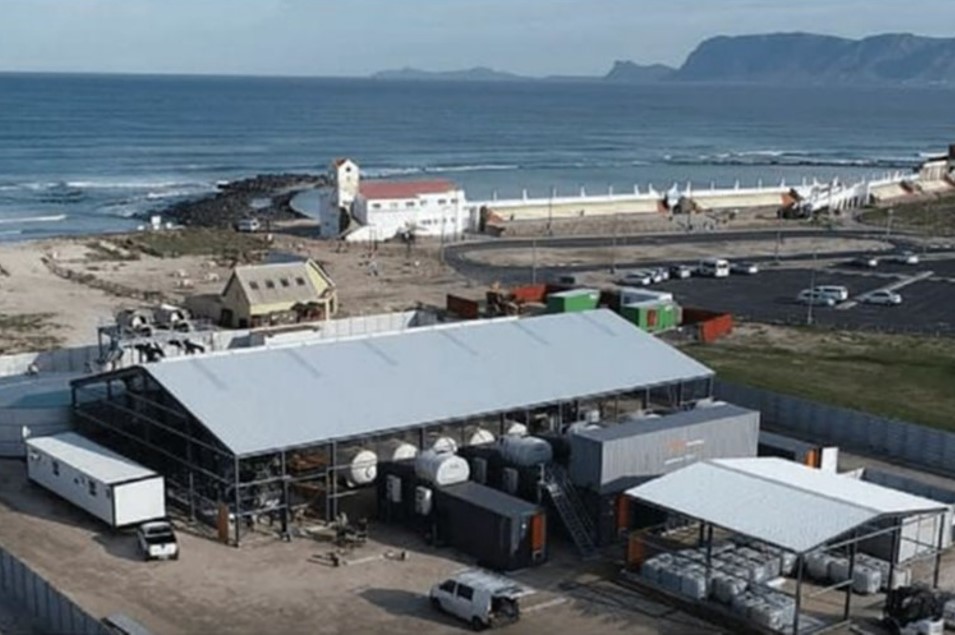
Sea Water Reverse Osmosis Plant Digitalization
The desalination plant was retrofitted with APRICOT™ by IntelliFlux to optimize the performance of the coagulant dosing and multimedia filtration (MMF) operations in response to fluctuations in influent seawater quality. Resulting in 35% Chemical savings, 44% lower Specific Energy Consumption (SEC). Learn More
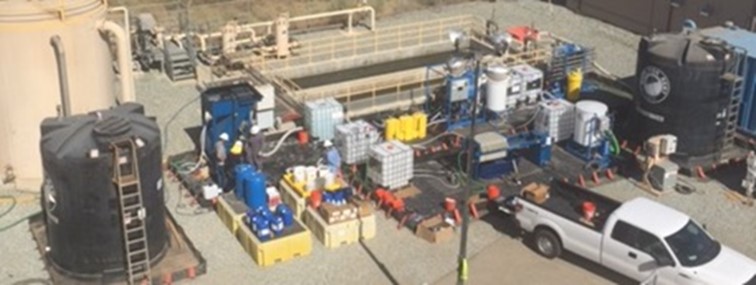
Industrial Water Management and Reuse
APRICOT™ by IntelliFlux was installed to optimize a treatment train including desilication chemical dosing, Inclined Plate Clarifier, UF and RO units through an integrated SCADA level automation platform with an objective of synergistically managing he precipitant dosage for the chemical desilication, monitoring the recycle rate of the UF to optimize the flosc for solid removal and managing the recovery of the RO process by maintaining a consistent RO feed quality. Click to see results. Learn More
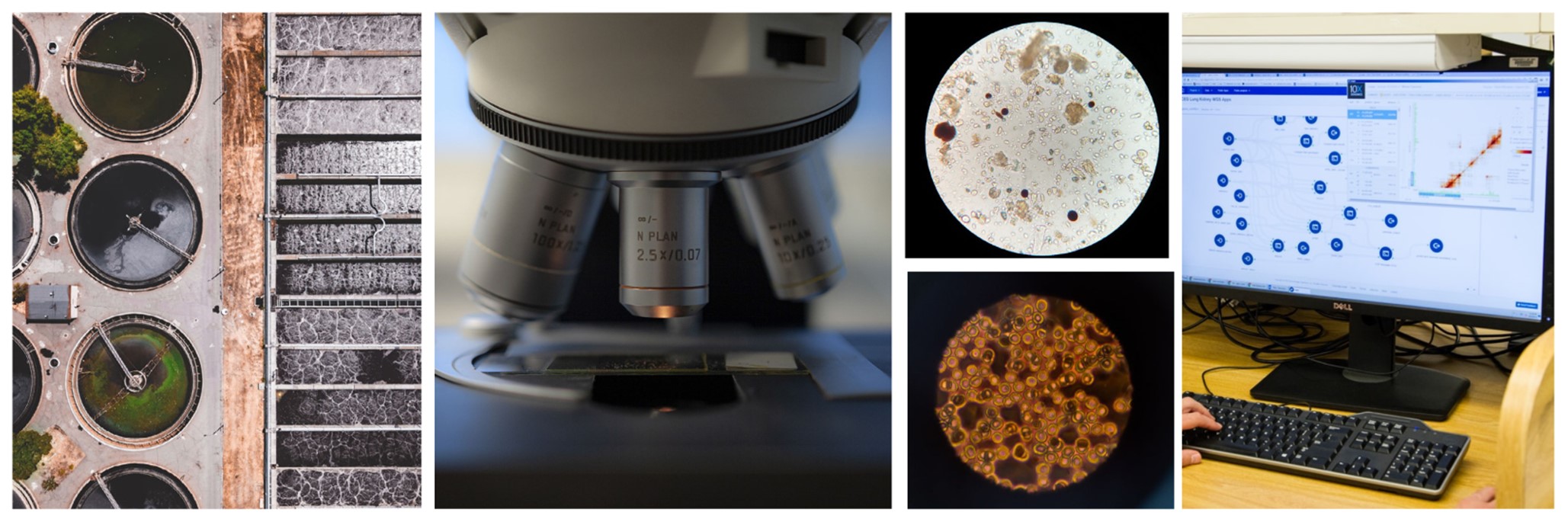
Automating Bioreactor Performance Recommendations from Sludge Microscopy Images
Samples of biomass are collected from the biological reactors at the wastewater treatment plant. APRICOT™ by IntelliFlux embeds learning algorithms to recognize feartures in the microscopy images, links therese to the microbial population health and a relate these to the reactor operating conditions. The software immediately provides an assessment of the image, indicating the condition of the microcosm in the reactor, and recommendations for process management. Learn More
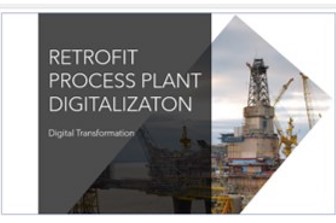
Retrofit Digitalization—Digital Transformation
Outlines the benefits to be gained by the process industry from a planned digitalization initiative. What is digitalization? We are smart plants? Industry 4.0 envisions the use of Internet of Things (IoT) and cyber physical systems such as sensors, actuators, vision system and robotics to collect and use plant information in a realtime manner by manufactureres to increase production efficiency. Learn More
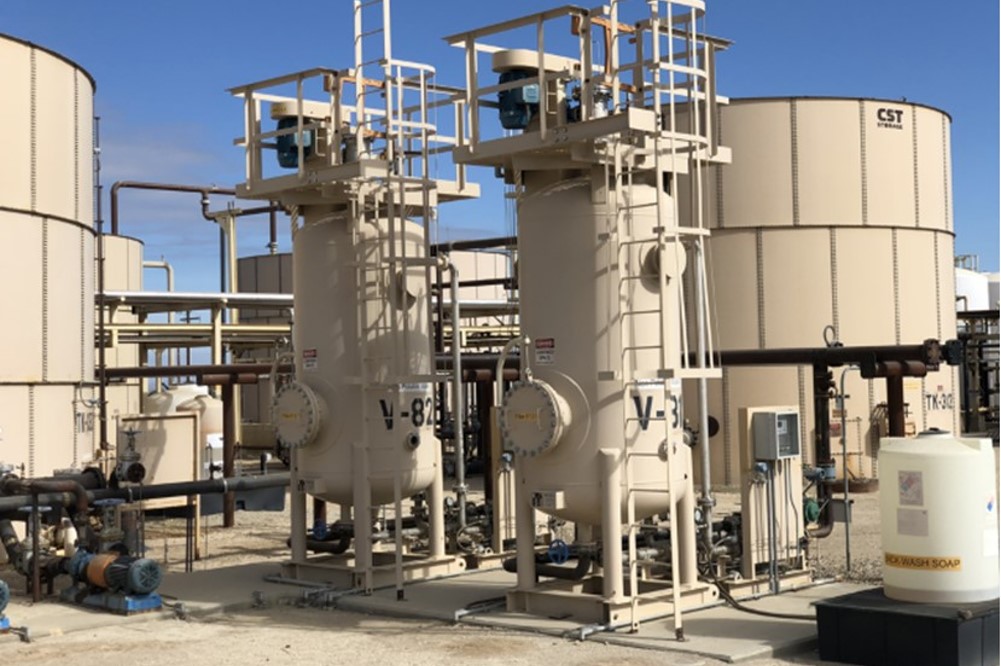
Autonomous Walnut Shell Filtration Optimization in Oil and Gas Industry
6000 bbl/day capacity walnut shell filtration system was retrofitted with APRICOT™ by IntelliFlux to optimize the filter performance and media cleaning process in response to fluctuations in influent produced water quality. Resulting in 47% energy reduction and 40% waste reduction in cleaning and ultimately a 5% increase in Uptime. Learn More
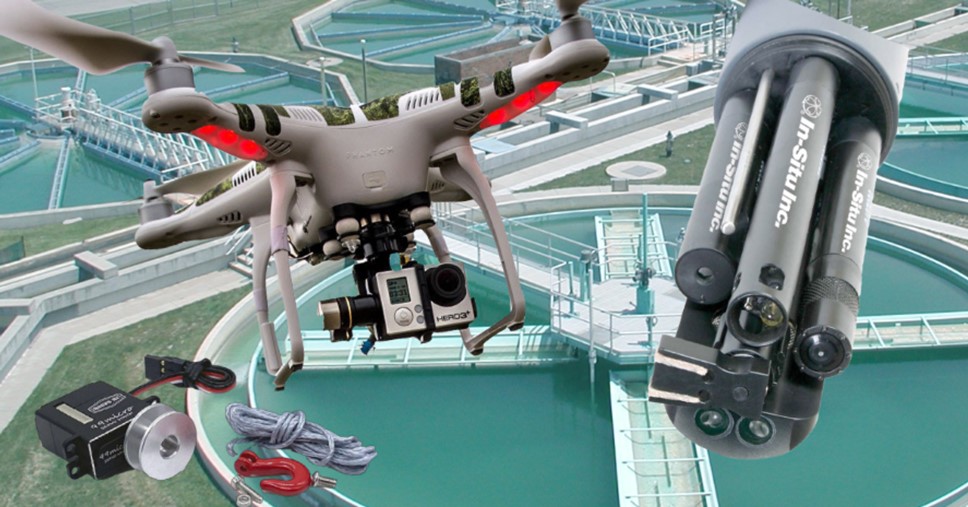
Drone Based Process Monitoring can Enhance Reliability
Replaces many sensors with a single one that can travel and take measurements at multiple locations on its own. The drone takes a pre-programmed flight path, stopping at locations where measurements need to be made. At each measurement site, the sonde is dipped into the desired depth of the tank or basin, the data reading is recorded and sent to a database with pro spatio-temporal signatures. Resulting in lower sensor cost and maintenance, less risk and more reliable results. Learn More
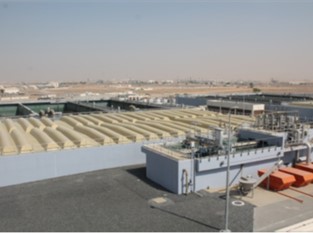
Biological Treatment Optimization at Municipal Plant
APRICOT™ by IntelliFlux was installed on a customer's 15,000 m3/day capacity SBR as an automation retrofit to optimize the treatment performance and increase the throughput of the system. IntelliFlux utilized the system's inline COD, TSS, Turbidity, NO3-N2, and Dissolved Oxygen (DO) sensors. Resulting in 28% increaase in Throughput and 45% savings in Energy per cycle Learn More
Contact us for a demonstration of our software today
We would love to hear from you to discuss how IntelliFlux can help your existing or upcoming process facility or system upgrade.