Apricot Operate
Real-time Autonomous Process Optimization
What is IntelliFlux
IntelliFlux is a technology powering the evolution of process control Artificial Intelligence and data exchange.
It is a seamlessly integrated platform linking the classical process control layers (like DCS, PLC, SCADA), and the higher level process digitalization frameworks embedded in the Industrie 4.0 design philosophy (IoT, interoperability, decision support, and decision automation).
At its core, IntelliFlux is a smart supervisory control and data acquisition (smart-SCADA) automation upgrade delivered through an edge control & communication device (ECD) and proprietary software. The software can be customized for specific primary automation hardware, process, or plant. The unique architecture of IntelliFlux software enables real-time process monitoring, learning about the process behavior, and developing a knowledgebase that can perform complex decisionmaking related to process optimization. IntelliFlux provides insightful assistance, guidance, and support to your operations team.
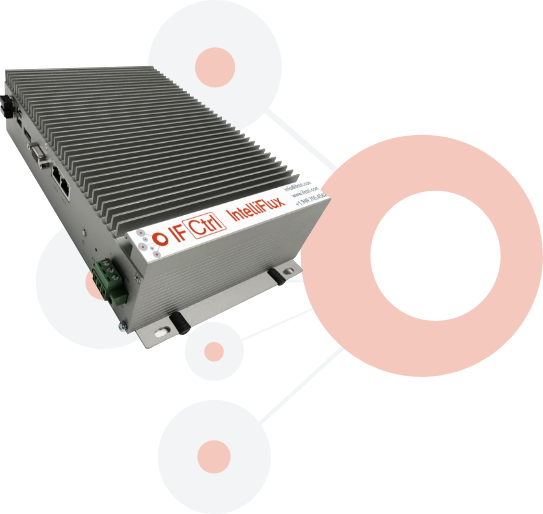
How IntelliFlux Works
IntelliFlux ECD is an interface consisting of a hardware module and software package pre-configured for your plant before it arrives. There is no need to add new control hardware. The IntelliFlux ECD is connected to your existing plant’s PLC/SCADA control platform. Once commissioned, the self-learning system continuously monitors and learns about how the plant operates and what interventions are required to maximize the plant’s productivity. From the moment it is switched on, IntelliFlux analyzes all the data it collects from your plant and continuously determines the causes and effects dictating the plant’s performance variations. This learning leads to identification of areas for optimization and improvement. The knowldge outputs are provided to operators and engineers managing the plant in real-time. Furthermore, within the bounds defined by operators, IntelliFlux can adjust the control setpoints autonomously. Utilizing this feature, the system optimizes the plant performance in response to any perturbation, improving your system reliability. Your operations team receives unprecedented foresight and insight about the process, helping them proactively improve and enhance the operations at the plant – even remotely. With IntelliFlux, you and your operations team get a more reliable plant with the ability to monitor and control it from anywhere, anytime.
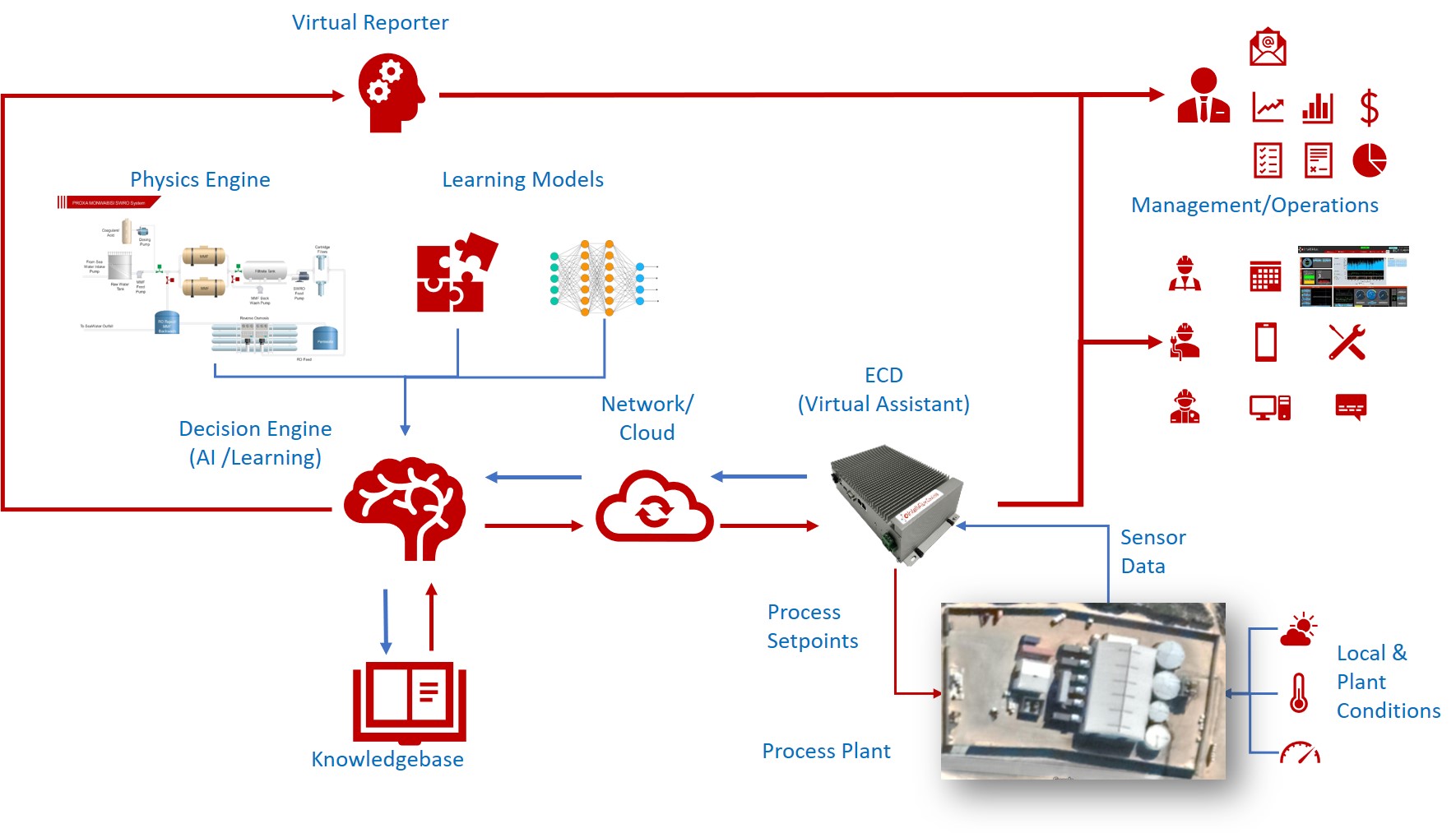
The IntelliFlux control system works in a supervisory role with your existing control system. It is a smart interface between the basic control layer of your plant and the operations team. Your operator / engineer can decide to activate or deactivate the autonomous control mode of Intelliflux. If the IntelliFlux system is taken offline, then your plant immediately reverts to the pre-existing automation and control framework without operational interruption.
FEATURES
Overnight transformation of an existing process plant into a smart plant. IntelliFlux provides one of the fastest, least disruptive, and non-invasive approaches of improving the plant productivity. No production disruption occurs during installation of IntelliFlux.
Immediate upgrade of the plant to a smart plant stature as the software features the complete Industry 4.0 digitalization stack. The functionalities range from real-time decision automation to machine learning based adaptive process optimization.
Can be configured for any commercially available brand of PLC and compatible with most standard industrial communication protocols used in DCS and SCADA systems. Single edge control and communication device can be connected to existing PLCs controlling multiple units at a plant.
Provides a comprehensive reporting tool, automated daily / weekly reporting features, and customized operator dashboards, so that authenticated operators and operations teams can monitor and even manage a plant operation
remotely.
BENEFITS

Sustainability
Lower specific energy consumption at the plant, higher energy efficiency, arrest depreciation profile of plant asset, sustainable operation.

Productivity
Increased production uptime of plants, higher throughput, less downtime and requirement of manual intervention.

Reliability
Improved reliability, reduced chances of catastrophic failure or fouling of process technology components, reduced maintenance downtime.

Profitability
Improved operating cost margins, manifested through savings in OpEx (less consumables, replacements, lower waste disposal costs, arrested margin erosion).